【ZiDongHua之创新自化成收录关键词:华中科技大学 东方电气 风机 永磁电机 矿山电机】
华科大首创的这一技术,再刷新“世界纪录”!
10月31日
华中科技大学
国家脉冲强磁场科学中心
工程技术团队
与东方电气集团
东方电机有限公司合作
成功实现了26兆瓦全球最大
单机功率风力发电机
原位退磁与退磁后的
再饱和充磁
这一技术突破对于
大型永磁电机退役回收后的
绿色再制造具有重要意义
这也是团队继2023年的成果之后
(《华科大这项技术,获广泛关注!》)
在该领域的又一突破
11月12日,我校党委宣传部、新闻中心与国家脉冲强磁场科学中心联合召开新闻发布会,对国家脉冲强磁场科学中心最新成果——大型永磁风力发电机无磁装配-原位整体充退磁一体化技术及装备进行介绍。
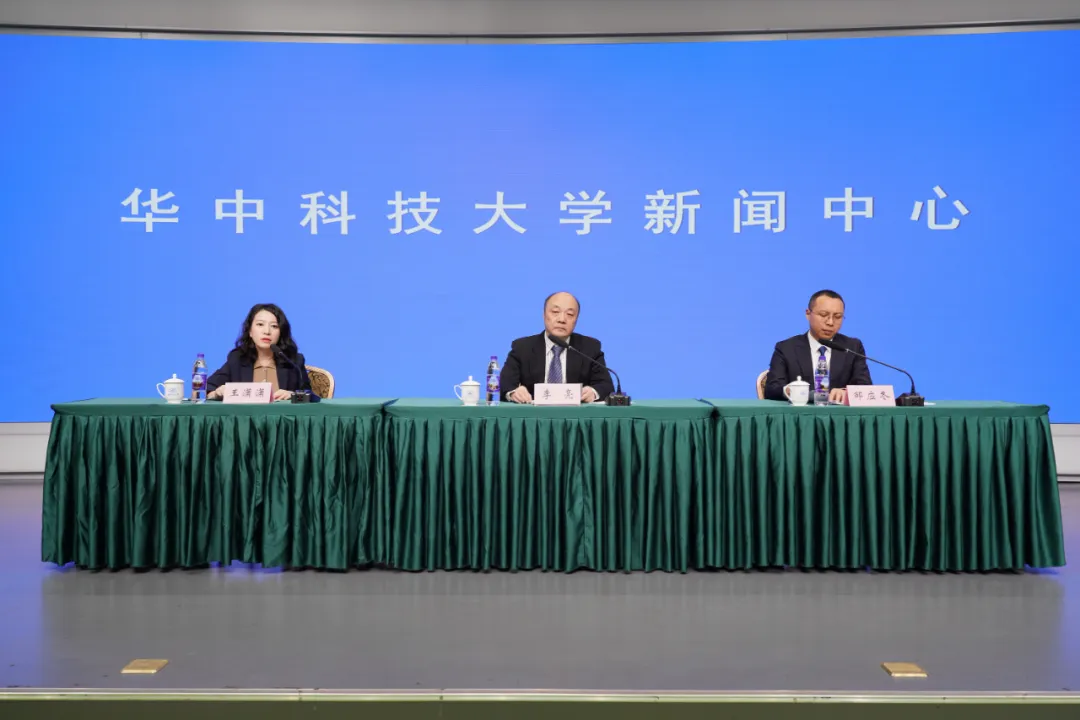
发布会上,国家脉冲强磁场科学中心主任李亮教授介绍了相关情况并答记者问。他表示,团队进行了十余年攻关,首创大型永磁电机“无磁装配-整体后充磁”方法,将常规电机制造的第一道工序——给单个永磁体逐块充磁,变成电机制造的最后一道工序即后充磁,突破大尺寸磁极整体充磁、复杂磁路约束下精准原位退磁及充退磁装备一体化等关键技术瓶颈,于2021年6月成功研制国内首套大型永磁电机整体充磁设备,2023年9月实现20兆瓦风力发电机转子的整体充磁,相关成果已成功应用于东方电机等企业2.5-20兆瓦全系列永磁风力发电机的制造,为企业带来了显著的经济效益,有助于推动我国风电绿色制造实现里程碑式高质量发展。相关技术是团队全体成员持续攻关、精益求精、团结协作的创新成果,同时也是团队依托脉冲强磁场国家重大科技基础设施,积极拓展强磁场技术应用、赋能新质生产力发展的成功尝试。
东方电气集团东方电机有限公司风电电机分公司党总支书记、副总经理邹应冬作为合作企业代表,现场回答了记者提问。他表示,东方电气拥有20年的风电装备研制经验,始终致力于为用户提供更加先进可靠的产品,其海上风电市场份额稳居行业头部,曾获得国家科学技术进步奖一等奖。作为集团风电电机产业承接企业,东方电机高度重视永磁风力发电机研制技术,包括稀土磁材的回收再制造技术。华中科技大学国家脉冲强磁场科学中心拥有一流的科研平台和雄厚的科研实力,李亮教授团队发明了整体充退磁一体化技术,正是企业所急需的技术。双方合作实现了26兆瓦风力发电机的原位退磁与再充磁,具有非常重要的工程应用价值。
关于这项技术
你想了解的更多信息
都在这里——
光明日报记者:团队研发的整体充退磁技术相比传统的技术方案,解决了哪些痛点难点问题?
国家脉冲强磁场科学中心主任李亮:永磁电机的制造、运维和退役回收再制造全过程的不同阶段,存在着不同的难点和痛点问题。
一是制造阶段。传统技术制造的过程中,需要先充磁后组装,永磁磁体间排斥力大,磁体极性要严格区分,容错率低。且由于制造全程带磁带力,因此安全性差,且磁极性能容易受到后续工序的影响,带磁动平衡校准难,制造质量、效率和性能都不稳定。而先无磁装配后充磁的技术则很好地解决了这些问题,除最后一道工序外,制造全程无磁场力,可以精准调节电机转子动平衡,制造效率可提高8-10倍,磁极性能、电机的机电性能和人身安全都得到了保证。
二是运维阶段。电机在运行过程中,会出现故障失磁、扫堂、堵转和腐蚀等问题,需要退磁拆卸和补充磁。传统的加热退磁技术,整机退磁需要把100-200吨的电机转子加热到300℃,并保温12个小时,这样将导致能耗大、污染严重,报废率极高。而采用我们的交流退磁技术,只需要不到200毫秒就能实现整极退磁,且能耗、污染、报废率和成本都极低。
三是回收再制造阶段。退磁后的磁极和永磁块能很方便地拆卸并能再利用、再加工、再制造。经过交流退磁的磁极再充磁至饱和所需的充磁磁场强度比常规的高出30%,我们的强磁场技术开发的充退磁一体化装备具备这个能力,这是其他技术无法企及的,能真正实现退役风机的绿色再制造。
科技日报记者:团队这项技术跟国际同行相比,有什么优势?
国家脉冲强磁场科学中心主任李亮:大型永磁风力发电机磁极体积大、极间距小,利用有限的电流空间在全磁极范围内产生饱和充磁磁场强度要求高,是整体充退磁技术的主要挑战,需要强大的脉冲强磁场技术基础。国外头部企业如GE和VESTAS等一直以来也在寻求这方面的技术突破,但目前只能将大磁极分段充磁,用独立的充磁系统先逐段充磁再逐段安装到位,没有真正解决先充磁后组装、制造全程带磁带力的痼疾。我们利用在国家重大科技基础设施脉冲强磁场大科学设施建设中发展起来的技术优势,解决了高电流密度脉冲强磁场的产生、强电磁冲击下脉冲线圈的多向加固、高重频快速冷却等技术瓶颈问题,实现了磁极整体原位后充磁,永磁电机先无磁高速、容错、高效装配,最后磁极整体充磁,技术可以应用于永磁电机生产线。
湖北日报记者:请问东方电机有限公司邹总,刚才李亮教授介绍了整体充退磁技术对即将到来的风力发电机大规模的退役潮具有重要作用,对此您有什么看法?
东方电气集团东方电机有限公司风电电机分公司党总支书记、副总经理邹应冬:风电行业一般按陆上机组20年寿命进行设计。预计在2025年,我国将会迎来风机退役高峰期。中国风能协会(CWEA)的数据显示,到2030年,累计有4473万千瓦风机进入退役期。而2010年至今,风机装机容量大幅攀升,仅2023年一年的新增装机就接近8000万千瓦。因此,未来将会有巨量的退役风电机组。而这其中,大量机组为永磁发电机。
面对如此巨大的退役潮,2023年国家发改委等部门出台政策,鼓励开展退役风电设备精细化拆解和高水平再生利用,重点聚焦发电机等部件。政府高度重视稀土材料回收,出台了一系列政策鼓励高效、节能、低污染、规模化的再生回收与综合利用。
像李亮教授刚才提到的,传统的风电磁钢回收采用物理粉碎、化学处理等方案,效率低、能耗高、经济效益差,且造成环境污染,因此,急需创新的技术和工艺,解决行业困难。
东方电气作为大型发电装备研制中央企业,拥有20年的风电装备研制经验,始终致力于为用户提供更加先进可靠的产品。企业海上风电市场份额稳居行业头部,曾获得国家科学技术进步奖一等奖。东方电气发电装备产量全球领先,将风电作为战略产业发展,主要采用永磁技术路线。因此,我们东方电机作为集团风电电机产业承接企业,高度重视永磁风力发电机研制技术,包括稀土磁材的回收再制造技术。
华中科技大学国家脉冲强磁场科学中心拥有一流的科研平台和雄厚的科研实力,李亮教授团队发明了整体充退磁一体化技术,正是我们所急需的技术。我们合作实现了26兆瓦风力发电机的原位退磁与再充磁,具有非常重要的工程应用价值。
应用整体充退磁一体化技术,磁钢退磁、完整拆解、精准加工、重新充磁赋能或者梯次再利用过程将变得非常高效、安全、环保和经济,这是其他技术方法完全无法企及的,是解决永磁风力发电机大规模退役绿色再制造困难的绝佳方案,不仅为企业发展新质生产力提供了有力支撑,对助推整个风电行业绿色制造高质量发展都具有非常重要的意义。
中国新闻社记者:除了在风机方面的应用,团队的整体充退磁技术还能应用在哪些领域?
国家脉冲强磁场科学中心主任李亮:除了风机方面,整体充退磁技术可以应用在几乎所有的永磁电气装备的制造、运维和回收再制造方面,如高速永磁电机、矿山电机、磁共振成像等方面。以高速电机为例,由于转子离心力大,需要热套一个高强度的不锈钢套筒来加固,充磁后的磁体性能容易受热套高温影响而降低,而先组装热套、后充磁就可以完美地解决这个问题。
整体充退磁技术不只是一个先进的工艺,也是一个新技术,传统技术下磁块和磁极无法再加工,磁极形状和气隙磁场位形无法调节,严重制约了装备的电磁性能。简单形状的永磁磁极只能用磁极表面的铁或铁芯的形状调节来获得精准的磁场位形,但这又会带来铁耗和温升,进而引起磁场的稳定度和均匀度的变化。先无磁装配后充磁,使磁块和磁极在无磁状态下能够被加工成任意形状,直接获得精准的磁场位形,表面没有铁,没有铁耗和温升,重量大大降低,提高了性能降低了成本。
总而言之,这种原位整体充退磁技术为永磁电气装备的设计、制造、运维、回收和绿色再制造提供了全新的技术途径。
为矢志创新、攻坚克难的
华科大团队点赞!
华中科技大学(ihuster)
来源/华科大新闻中心
评论排行