华创科技:石化行业质量智能检测领航者
华创科技:石化行业质量智能检测领航者
2024年12月30日,工信部联合市场监管总局公布了2024年度智能制造系统解决方案“揭榜挂帅”项目名单,全国共83个项目上榜,我市达美盛等8家企业项目成功揭榜。智能制造系统解决方案“揭榜挂帅”项目旨在面向重点行业数字化转型和智能化升级需求,聚焦智能工厂建设堵点痛点,培育一批专业化解决方案供应商,形成先进适用、自主可控、可复制推广的智能制造系统解决方案产品和服务并应用验证。
为进一步宣传推广我市智能制造系统解决方案优秀成果,市经济和信息化局特设“北京智造巡礼——解决方案篇”专栏,充分发挥揭榜单位供给能力,助力广大企业系统深入推进智能制造。
企业基本情况
北京华创中实科技发展有限公司(简称:华创科技)成立于2004年,主营业务包括实验室管理、实验室执行、质量管理、生产调度和管网优化等软件产品的研发、实施和服务。
华创科技专注于能源行业信息化建设,经过多年发展,拥有具有完全自主知识产权的实验室信息管理系统(HCT-LIMS)、实验室执行系统(HCT-LES)、生产调度与优化管理系统(SKI)、蒸汽管网节能优化系统(HCT-PO)等软件30余种。2024年,华创科技“面向石化化工行业的智能检测与质量追溯优化系统解决方案”入选工信部智能制造系统解决方案“揭榜挂帅”项目。
行业面临痛点
系统集成问题:质量领域软件往往需要与企业内部的多个异构系统进行集成,如ERP(企业资源计划)、MES(制造执行系统)、SCM(供应链管理)等。这些系统可能来自不同的供应商,采用不同的技术架构、数据格式和通信协议,导致集成时面临兼容性难题。
创新应用问题:现有软件与人工智能、机器学习等前沿技术的融合不够深入,软件的自学习、自适应能力不足;系统无法根据历史数据自动优化检测策略,调整质量评估模型,难以实时应对生产过程中的突发情况和工艺变化,数据挖掘与分析能力弱。
管理效率问题:传统的石油化工质量管理主要依赖人工检测,工作强度大,效率低;现有质量检测软件功能单一,难以满足石油化工企业复杂的质量管理需求;质量控制信息无法及时反馈到生产环节,导致质量问题难以及时纠正,影响产品质量的稳定性和一致性。
自主可控问题:石油化工行业质量检测与追溯软件长期依赖国外产品,同时,石油化工行业涉及大量敏感数据,存在安全隐患,亟需实现国产化替代。
核心应用场景
华创科技针对上述痛点,研发了具有自主知识产权的实验室信息管理系统、实验室执行系统、数据自动采集系统、机器人实验系统等,为石油化工行业质量管理提供了有力支撑。
(一)仪器智慧物联
通过采用物联网技术,将各种仪器设备连接到物联网平台,实现数据的实时采集、传输和分析,实现智慧互联,提升数据的及时性、准确性和质量管理的效率;通过实时分析生产过程中的各类数据,如温度、压力、流量等工艺参数,以及原材料的质量指标,精准控制产品质量。
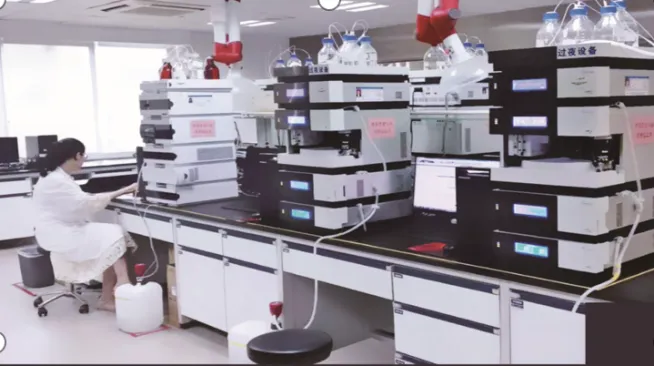
(二)机器人智能实验
运用传感器技术在检测设备和关键节点部署各类传感器,采集各类质量指标数据;采用AGV机器人技术、先进的导航技术,精准定位并自动规划路径,满足实验过程中不同类型样品的转运需求,实现实验过程中的自动分样、送样和上样;采用大数据分析和人工智能算法对采集数据进行分析,通过与预设标准对比及历史数据学习,提前预警潜在质量风险,对分析检测数据的有效性、准确性进行进行智能自动审核判定。
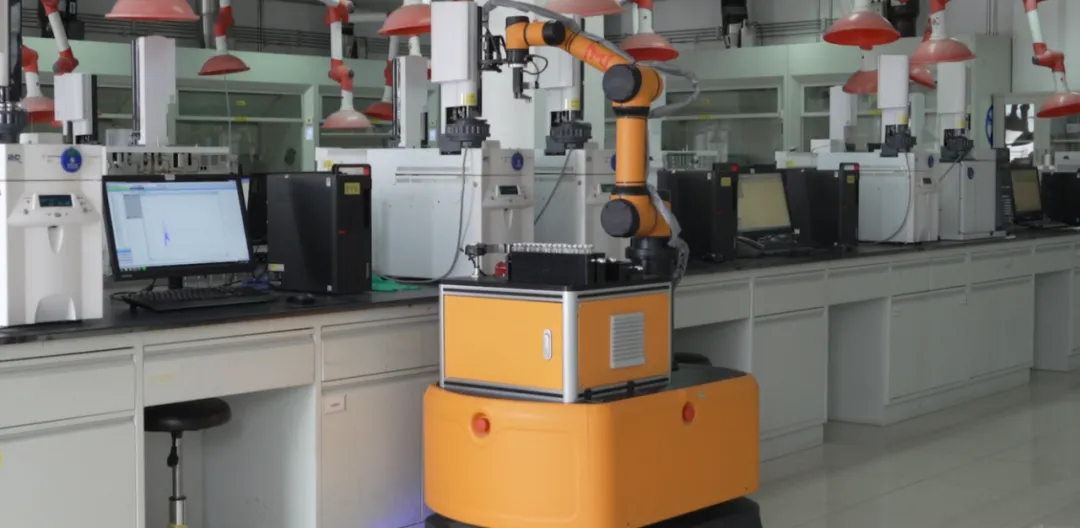
(三)质量追溯协同
实现从原材料采购、生产加工、包装存储到产品销售的全生命周期质量追溯,快速、准确地追踪到产品的每一个环节和相关信息。当出现产品质量问题时,迅速定位问题源头,企业及时召回、整改,减少损失;强化对供应链的质量管控,使企业更清晰地了解原材料供应商的质量状况和生产过程,确保了原材料的质量。同时,便于企业与供应商、客户之间进行信息共享和协同合作,共同提升整个供应链的质量水平。
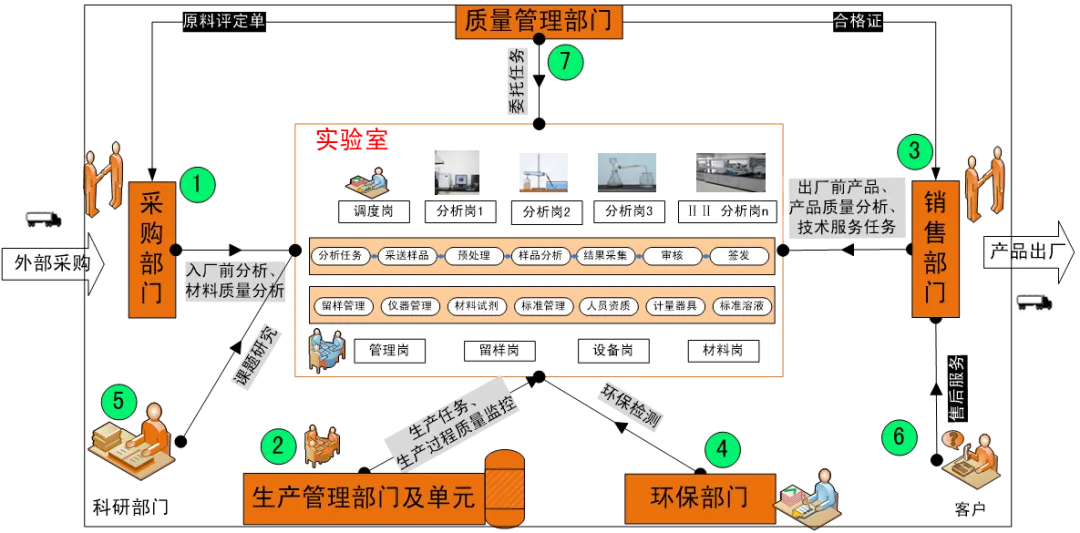
(四)质量管理与优化
采用大数据技术深度挖掘质量数据,并根据原因分析结果自动生成工艺改进建议,如优化操作流程、调整设备参数等;利用人工智能技术,对质量数据进行深度分析和趋势预测,提前发现潜在质量问题,发出预警信号,及时采取预防措施,避免损失扩大;通过对质量追溯数据的分析,找出生产过程中影响产品质量的关键因素,为企业提供工艺改进建议,优化生产工艺,提升产品质量。
推广应用成效
华创科技已承建中国石油化工集团有限公司、中国石油天然气集团有限公司、中国海油集团有限公司等企业近千个实验室的质量管理信息系统建设,成效显著。
(一)实现全流程体系管控
实现分析全流程,包括实验条件、实验要素、实验步骤、装置、采样点、产品标准等信息源的采集、传输;实现了分析过程中人流、物流和设备流的互联互通;实现了采集标准、解析规则的统一,实现从样品来源到报告生成的分析实验全流程标准规范。
(二)实现实验要素数智化管理
按照ISO/EC・17025管理要求,结合石化企业业务特点,引入了标准曲线、标准溶液、计量器具、样品留样、仪器设备、实验人员、实验环境、实验标准、实验料剂等辅助分析模块,对实验要素进行全面量化管理,实现实验资源的优化配置。同时,规范了企业从原料入厂、中间过程到产品出厂业务的分析业务流程,将分析任务的发起、样品检测、数据计算与修约、审核,以及数据发布、任务处理等实验过程与人机料法环等实验要素深度融合,确保各环节严格遵循标准,保障石化产品质量管控的科学性和可靠性。
(三)实现质量预测预警管理
通过质量系统建设,形成了完善的质量预警管理机制,包括预警指标的设定、预警信息的收集与分析、预警措施的制定与实施等;通过实时监控生产过程中的关键质量参数和工艺参数,及时发现潜在的质量问题,确保产品质量的稳定性和一致性。
(四)实现机器人智能实验
采用智能分样设施和AGV机器人技术,实现一次样品推入系统后的自动接收、开盖、移液、关盖、搬运、扫描、识别和二次样品赋码、进样、检测以及结果的自动上传;建立智能审核模型,实现了智能审核,及时预警检验过程中的不合格数据,降低实验人员的工作量和劳动强度,实验效率提升了10%以上。
我要收藏
点个赞吧
平台转发数:1次
评论排行