科技新进展:鞍钢智慧高炉大数据可视化平台建设与示范应用
科技新进展:鞍钢智慧高炉大数据可视化平台建设与示范应用
一、研究的背景与问题
《中国制造2025发展规划》明确要求传统的制造业要向数字化、网络化、智能化、绿色化发展,支持传统产业优化升级,尤其是钢铁行业依靠信息化、智能化技术,把传统的钢铁企业转型成智能制造企业。在钢铁工业中高炉的生产成本、能源消耗、CO2排放量均占70%以上,是制约钢铁行业竞争力的瓶颈。由于高炉及其附属工序设备工艺多样复杂性、生产过程不确定性,以及所有变化过程均发生在大封闭性的高炉内部,难以直接检测,属于典型“黑箱”问题,到目前为止,高炉操作依然是以高炉操作者经验为主,难以做到高炉长期高效低耗和炉况稳定顺行。鞍钢高炉众多,高炉群也难以被统一管理。因此迫切需要建设资源共享、优势互补、高效协同的大数据集约化与可视化管控平台,以提升高炉群整体协同效率。
鞍钢高炉及其附属工序之间多工序和各高炉之间在一体化管理方面存在的一些难题:一是缺少统一智能化管理平台,炉况、生产信息零散不集中,分散独立,数据共享和分析挖掘不够。二是协同响应滞后,由于时空阻隔,协同信息、需求信息滞后;部分信息经层层过滤,准确性、及时性受限。三是缺少统一的评价体系,由于高炉群工艺装备、原燃料、操作模式的差异,指标先进性、运行状态评价体系不一致。四是语言、标准尚未完全统一,一些工艺参数名称、计算方法、异常炉况的判别、操作应对标准、各高炉操作手法与偏好不一致。
基于以上背景与需要,鞍钢从2007年开始,逐渐补充和完善炼铁产线上检测工业传感器的同时,积极同北京科技大学合作,从高炉冶炼机理和传输原理层面进行数学建模以揭示高炉“黑箱”内的反应及状态,为鞍钢两化融合实现智能化炼铁打下基础。近年来,通过大数据挖掘技术运用,开发了“鞍钢智慧高炉大数据可视化管控平台,实现了高炉群及附属工序数据资源共享、优势互补、高效协同的统一管理,并打通传统各级信息化系统之间的数据孤岛,完成高炉炼铁从智能单元到智能平台的升级。此外以高炉大数据平台为基础,从炼铁机理层面定制开发“一炉一策”高炉数学模型,开发高炉炉缸侵蚀状态3D可视化监控模型,建立基于数据挖掘高炉群炉况评价体系,对不同炉型高炉冶炼过程实施统筹智能管理,使得鞍钢炼铁工序全流程得到转型升级,极大提升高炉生产、技术与管理的数字化、科学化、智能化水平,完美实现高炉冶炼过程从“黑盒”向“白盒”的重要突破。
二、解决问题的思路与技术方案
根据鞍钢高炉的设计、生产和操作特点,基于冶金基础理论与人工智能前沿技术,定制开发高炉数学模型,实现高炉的高效生产,提升高炉生产、技术与管理的整体数字化、科学化、智能化水平,同步实现高炉炼铁的安全长寿、低耗高效、清洁生产,实现高炉冶炼从“黑盒”向“白盒”的重要突破。总体思路如图1所示:
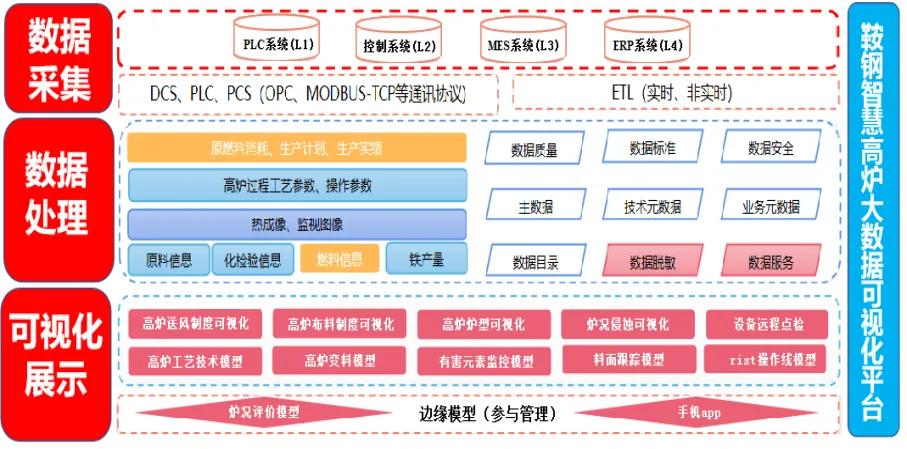
图1 项目研究总体思路图
1、建立高炉群生产大数据平台
建立高炉生产过程操作参数数据仓库、完成不同数据库的各种接口和数据统一表示,用于支撑外部数据采集、内部数据整合;利用控制系统所提供的OPC服务器功能,编写OPC客户端程序,实现从基础自动化系统中读取生产过程实时数据。高炉生产过程信息化、智能化平台建设项目结合物联网建设,数据采集、通讯、数据清洗、数据预处理、数据分类、存储等建立数据平台和大数据处理中心,为基于数据平台开发工艺机理和统计数学模型、大数据分析与挖掘、机器学习、专家系统等提供保障,同时满足厂长、厂调度、公司调度及其他管理及科研部门的需求。
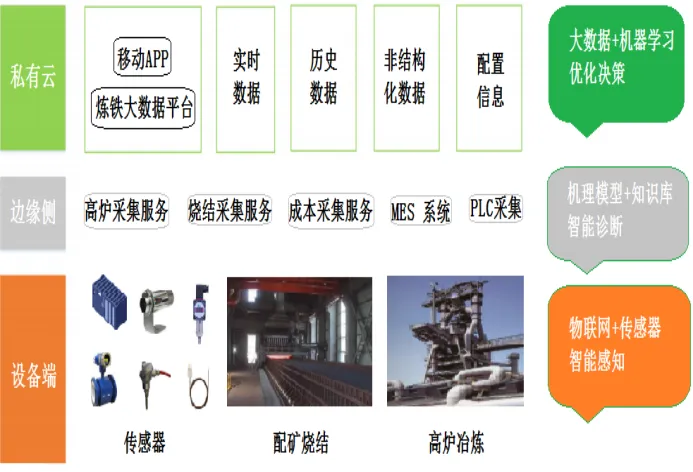
图2 鞍钢高炉大数据平台构架
2、基于高炉大数据平台的高炉“一炉一策”可视化平台开发
高炉机理建模与数字化仿真系统融合机理的全高炉综合数学模型,实现全高炉仿真和工作状态精确解析,提供高炉炉况预测结果和匹配操作的推送、完成高炉操作变更影响因素的推送、完成高炉运行趋势分析结果的推送和历史数据溯源结果的推送。
3、高炉炉缸炉底多维冗余侵蚀计算模型和结构安全指标预警机制评估系统
以鞍钢不同炉容高炉炉缸的破损调查为基础,综合检测不同种类炭砖;并建立炭砖合理的评价制度;利用高炉破损调查结果不断深入的校正计算模型。
4、基于数据挖掘的高炉健康状态的评价体系
挖掘影响高炉生产和操作的主因、隐因以及高炉操作关联,研究高炉冶炼参数的关联分析、高炉操作规则的关联分析和历史数据溯源。高炉大数据全流程挖掘与云计算。将历史数据与当前操作关联,实现高炉生产过程多种操作参数优化,推算最佳高炉工艺路线。
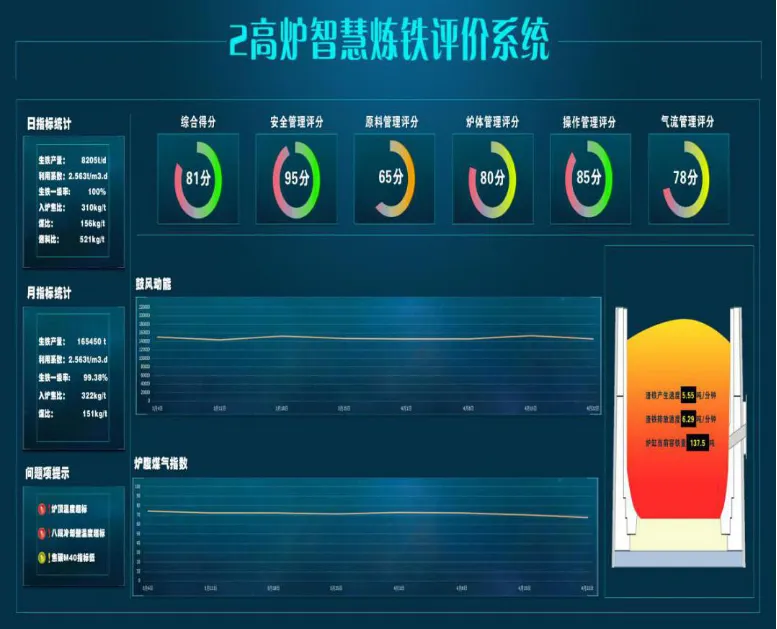
图3 关键参数预警诊断系统
三、主要创新性成果
1、建立鞍钢高炉群大数据平台
基于工业物联网、云存储、云计算等技术完成高炉及附属工序、MES系统、ERP系统数据整合,打破信息孤岛,建立以高炉群为核心的大数据集约化管控平台,实现高炉生产状态的全息再现。
2、建立高炉“一炉一策”可视化平台
在高炉大数据云平台交互基础上开发高炉生产工艺模型和移动终端APP,对高炉冶炼全过程进行全方位、实时可视化监控。实现高炉生产全流程物质流与能量流信息化管控、高炉操作炉型和冷却壁安全监测与预警、高炉装料及布料过程智能仿真、炉顶料面与煤气流分布及风口回旋区的三维可视化监控。
3、鞍钢高炉炉缸侵蚀状态高精度预判及三维可视化监控模型开发与应用
基于高炉破损调查炭砖特征和性能指标检验结果,修订炭砖捣料的导热系数,建立高精度高炉炭砖残厚计算数学模型,并利用计算机图形学技术对数据结果作处理,实现了炉缸内衬侵蚀程度的精准判断和侵蚀形貌的循环动态展示。
4、建立基于数据挖掘高炉群炉况评价体系
对高炉冶炼全流程进行数据挖掘与深度解析,建立高炉冶炼参数与高炉经济技术指标的关联性评价体系,实时对高炉的健康状况进行打分并做出智能诊断和优化建议。
四、应用情况与效果
本项目成果已在鞍钢本部炼铁总厂2号、3号高炉(3200m3)、5号高炉(2580m3)和鲅鱼圈分公司炼铁部1号、2号高炉(4038m3)实施应用,同时炼铁总厂1号、2号、3号、10号高炉(3200m3)4号、5号高炉(2580m3)初步实现集控功能,从生产、操作、技术、管理、培训等全方位提升鞍钢炼铁的数字化、科学化、智能化、标准化水平,取得如下效果:
(1)将遥感测温、三维激光雷达、热成像等新技术应用于传统炼铁工业传感及物联网开发,实现对高炉群、烧结机、球团机等炼铁核心设备及大数据的在线监测,达到了减少较危险的点检和炉前工作对人的依赖,降低了安全事故发生率;
(2)建立基于工艺机理、大数据、机器学习、互联网+的配矿、烧结、球团、高炉智能控制系统的炼铁大数据智能可视化与集控平台实现鞍钢高炉群各产线炼铁数据互联互通和复杂的铁前各工序高效协同,高炉操作人员劳动生产率提高44%;
(3)建立高炉冶炼过程可视化云平台及移动终端APP高炉诊断模式,初步建立“炼铁移动工厂”,冶炼取得了从“黑盒”向“白盒”的重要突破,炼铁操作和炉况分析由原先依靠人工经验和主观判断为主转变为依靠数据为主,项目实施后,本部炼铁总厂2、3、5号高炉和鲅鱼圈炼铁部1、2号高炉在入炉品位较低、大量使用外购焦和湿熄焦条件下,5座高炉利用系数平均提升0.487t/(m3·d),指标达到国内先进水平。
截止目前,本成果授权发明专利14件,登记软件著作权4项,发表高水平研究论文28篇。
信息来源:鞍钢股份有限公司
我要收藏
点个赞吧
平台转发数:1次
评论排行